The Essential Guide to Process Optimization in Semiconductor Manufacturing
- AAAPlus Automation
- Apr 24, 2024
- 4 min read
Understanding the Basics of Semiconductor Manufacturing
In semiconductor manufacturing, tiny electronic components are produced on a silicon wafer. The basic steps of this process involve designing the electronic circuit, creating a mask, exposing the wafer to light through the mask, etching the pattern on the wafer, and testing the final product for quality assurance. Clean rooms are used to ensure a dust-free environment for manufacturing. Silicon is the most commonly used material due to its semiconductor properties.
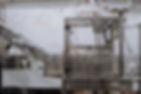
Importance of Process Optimization in Semiconductor Industry
Process optimization is crucial in the semiconductor industry to enhance efficiency and reduce costs. By fine-tuning production processes, semiconductor manufacturers can improve product quality, increase yield, and shorten manufacturing times. Optimized processes lead to higher productivity, better resource utilization, and overall enhanced competitiveness in the market. It is vital for semiconductor companies to continuously analyze and refine their processes to stay ahead in this rapidly evolving industry.
Key Challenges in Semiconductor Manufacturing
Semiconductor manufacturing faces various challenges that can impact the efficiency of the overall process. Here are some key challenges to be aware of:
Complexity of Processes: Semiconductor manufacturing involves intricate processes that require precision and expertise, making it challenging to optimize workflow.
Cost Constraints: The high cost of equipment and materials in semiconductor manufacturing can pose a challenge to companies looking to streamline their processes while maintaining profitability.
Technology Advancements: The constant evolution of technology in the semiconductor industry means manufacturers need to adapt quickly to stay competitive, which can be a challenging task.
Quality Control: Ensuring consistent quality in semiconductor production is crucial but can be challenging due to the sensitivity of the materials and the complexity of the processes involved.
Introduction to Process Optimization
Process optimization in semiconductor manufacturing is crucial for enhancing efficiency and reducing costs. By fine-tuning production processes, companies can maximize output and minimize waste. It involves analyzing and improving each step of the manufacturing process to streamline operations. Key benefits of process optimization include improved product quality, faster production cycles, and increased profitability. Factors such as equipment efficiency, resource allocation, and technology advancements play a significant role in achieving optimal results.
Tools and Techniques for Process Optimization
When optimizing processes in semiconductor manufacturing, there are various tools and techniques that can be employed. These include statistical process control, Six Sigma methodologies, root cause analysis, and machine learning algorithms. By utilizing these tools, manufacturers can identify inefficiencies, minimize defects, and improve overall production quality.
Implementing Lean Principles in Semiconductor Manufacturing
To implement Lean principles in semiconductor manufacturing, you must focus on reducing waste and maximizing efficiency in your processes. Consider these key steps:
Identify and eliminate waste:Â Look for inefficiencies in your processes such as waiting times, unnecessary movements, overproduction, or excess inventory.
Implement a continuous improvement mindset:Â Encourage your team to constantly seek ways to streamline operations and enhance productivity.
Standardize processes:Â Establish clear protocols and procedures to ensure consistency and reliability in manufacturing.
Empower employees:Â Involve your workforce in decision-making and problem-solving to foster a culture of ownership and innovation.
Monitor performance:Â Use key performance indicators to track progress and identify areas for further optimization.
By incorporating these Lean principles into your semiconductor manufacturing operations, you can enhance efficiency, reduce costs, and improve overall quality.
Impact of Process Optimization on Efficiency and Quality
Optimizing processes in semiconductor manufacturing can significantly improve both efficiency and quality. By streamlining procedures and identifying areas for enhancement, manufacturers can reduce errors, minimize waste, and enhance overall production outcomes. Efficient processes also often result in higher-quality products, as optimized workflows tend to be more consistent and predictable. This ultimately leads to increased productivity and customer satisfaction.
Case Studies of Successful Process Optimization in Semiconductor Industry
Successful process optimization in the semiconductor industry has been achieved through various case studies. Here are some examples of how companies have improved their processes:
Company A: Reduced production time by 20% by implementing new automation technologies.
Company B: Achieved a 15% increase in product quality by fine-tuning their manufacturing processes.
Company C: Cut down waste by 30% through the implementation of lean management principles.
Company D: Improved overall efficiency by 25% by reorganizing their production line layout.
Future Trends in Process Optimization for Semiconductor Manufacturing
Future trends in process optimization for semiconductor manufacturing are constantly evolving to meet the industry's demands. Here are some key points to keep in mind about where the field is heading:
The integration of artificial intelligence (AI) and machine learning algorithms is expected to play a significant role in enhancing process efficiency and yield rates.
Advancements in Internet of Things (IoT) technology will enable real-time monitoring and control of manufacturing processes, leading to proactive maintenance and improved overall productivity.
The adoption of advanced data analytics tools will empower companies to make data-driven decisions, optimize production workflows, and reduce operational costs.
Continued focus on sustainability and environmental impact will drive the development of green manufacturing processes, such as energy-efficient technologies and waste reduction strategies.
Collaboration across the supply chain and partnerships with technology providers will be crucial in driving innovation and staying ahead in the competitive semiconductor manufacturing landscape.
Conclusion and Key Takeaways
After implementing process optimization in semiconductor manufacturing, it is crucial to consider some key takeaways. Here are the main points to remember from this guide:
Continuous Improvement: Process optimization is an ongoing effort that requires regular monitoring and adjustments.
Data-Driven Decisions: Utilize data analytics to make informed decisions and identify areas for improvement.
Collaboration is Key: Encourage teamwork and open communication among departments to streamline processes.
Invest in Training: Ensure employees are properly trained to implement and maintain optimized processes.
Stay Up-to-Date: Keep abreast of new technologies and industry trends to remain competitive.
Monitor Results: Regularly assess the impact of process optimization on efficiency, cost savings, and quality.
Celebrate Successes: Recognize and reward achievements to motivate employees and maintain momentum.
In conclusion, by following these key takeaways, semiconductor manufacturers can enhance productivity, reduce costs, and stay ahead in the ever-evolving industry landscape.